Building an Energy Harvesting Device from Kinetic Motion
An energy harvesting device captures energy from kinetic motion (such as human movement, vibrations, or machinery) and converts it into electrical power. Such devices are ideal for powering small electronics, sensors, or low-power IoT devices, especially in off-grid or resource-constrained environments.
1. Objectives and Goals
- Primary Purpose: Harness kinetic energy from motion and convert it into usable electrical energy.
- Key Features:
- Efficient energy conversion and storage.
- Portable and robust design for diverse applications.
- Low-cost and scalable for various use cases.
- Target Audience: Engineers, hobbyists, and researchers in sustainable energy.
2. Key Components
A. Kinetic Energy Source
- Human Motion: Walking, running, or arm movements.
- Vibrations: From vehicles, machinery, or infrastructure.
- Rotational Motion: Spinning wheels or gears.
B. Energy Conversion Mechanism
- Piezoelectric Materials:
- Generate electricity when mechanically deformed.
- Suitable for applications involving small vibrations or pressure.
- Examples: Piezoelectric plates, patches, or crystals.
- Electromagnetic Induction:
- Converts motion into electricity using magnets and coils.
- Example: A small generator where motion causes a magnet to move relative to a coil.
- Triboelectric Nanogenerators (TENGs):
- Harvest energy from friction or sliding surfaces.
C. Energy Storage
- Rechargeable batteries (e.g., lithium-ion or nickel-metal hydride).
- Supercapacitors for quick charging and discharging.
- Direct powering of low-power devices (if applicable).
D. Power Management Circuit
- Rectifier: Converts AC from the generator to DC for storage.
- Voltage Regulator: Maintains a stable output voltage for the device.
- Energy Management IC: Optimizes energy harvesting and storage.
E. Housing and Mounting
- Durable enclosure to protect components.
- Attachments for integration with moving parts or wearable setups.
3. Design and Implementation Steps
A. Define the Application
- Determine the type of kinetic motion to be harnessed.
- Examples:
- A wearable device powered by walking.
- A vibration-powered sensor on machinery.
B. Select Energy Conversion Mechanism
- For small, consistent vibrations, use piezoelectric materials.
- For larger motions, such as swinging or rotational motion, use electromagnetic induction.
- For friction-heavy environments, consider triboelectric nanogenerators.
C. Build the Energy Converter
- Piezoelectric Setup:
- Attach piezoelectric elements to a flexible base.
- Connect elements in series or parallel to increase output.
- Electromagnetic Induction:
- Assemble a coil and magnet.
- Design a mechanism (e.g., spring or pendulum) to move the magnet relative to the coil.
- TENG Setup:
- Use two surfaces with different triboelectric properties.
- Ensure consistent contact and separation during motion.
D. Assemble the Power Management Circuit
- Use a diode bridge rectifier to convert AC to DC (if needed).
- Add a capacitor to smooth out voltage fluctuations.
- Integrate a voltage regulator to protect the storage device.
E. Test and Optimize
- Measure the output voltage and current under expected motion conditions.
- Adjust the design (e.g., more coils, better alignment) for higher efficiency.
- Test the storage and delivery system to ensure stable output.
4. Example Applications
- Wearable Devices:
- Install piezoelectric strips in shoe soles to charge small devices like pedometers or fitness trackers.
- Vibration-Powered Sensors:
- Attach an electromagnetic generator to a vibrating machine to power condition-monitoring sensors.
- Rotational Systems:
- Use a small dynamo in bicycle wheels to charge lights or mobile devices.
5. Advantages
- Sustainability: Reduces reliance on disposable batteries.
- Versatility: Applicable in various environments and scales.
- Energy Efficiency: Converts otherwise wasted motion into power.
6. Limitations
- Output power is typically low, suitable for small devices only.
- Efficiency depends on motion consistency and energy conversion mechanism.
- Requires careful design to balance durability and performance.
7. Cost Estimate
- Energy Converter:
- Piezoelectric materials: $10–$30.
- Magnet and coil (electromagnetic): $10–$25.
- TENG materials: $10–$20.
- Power Management Circuit: $10–$20.
- Storage Device: $10–$30.
- Enclosure and Accessories: $10–$20.
- Total Cost: $40–$100.
8. Future Enhancements
- Integrate wireless charging for connected devices.
- Scale up the design for higher power applications.
- Use advanced materials to increase energy conversion efficiency.
Would you like assistance with specific aspects, such as circuit design, material selection, or application integration?
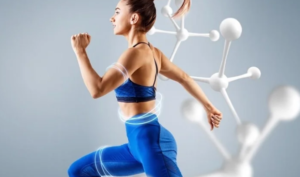
Also Read :