In the fast-paced evolution of modern industry, advanced manufacturing techniques are driving innovation, productivity, and sustainability. At the core of many of these advancements lies a single, versatile material—titanium. With its unique balance of strength, low density, biocompatibility, and resistance to extreme environments, titanium has become an essential material in shaping the future of aerospace, automotive, medical, and additive manufacturing sectors.
This article explores how titanium is transforming advanced manufacturing techniques, enabling breakthroughs that were once considered science fiction. From cutting-edge 3D printing technologies to high-performance precision machining, titanium is empowering engineers, scientists, and manufacturers to push the boundaries of what’s possible.
Why Titanium Is Ideal for Advanced Manufacturing
Titanium isn’t just another metal—it’s a strategic material with properties that make it ideal for high-performance, next-generation manufacturing.
Key Properties of Titanium:
- High strength-to-weight ratio – Stronger than many steels but significantly lighter
- Corrosion resistance – Withstands aggressive environments, including seawater and body fluids
- Heat resistance – Retains strength at high temperatures
- Biocompatibility – Non-toxic and integrates well with human tissue
- Formability – Can be shaped, cast, welded, or 3D printed with specialized techniques
These properties make titanium indispensable in producing precision-engineered components, especially where reliability, longevity, and performance are non-negotiable.
Titanium in Additive Manufacturing (3D Printing)
Perhaps the most exciting area where titanium is making waves is in additive manufacturing, especially in metal 3D printing.
1. Titanium Powders in 3D Printing
Titanium alloys such as Ti-6Al-4V are widely used in powder bed fusion (PBF) and direct energy deposition (DED) 3D printing methods. These processes allow engineers to:
- Create complex geometries that are impossible with traditional machining
- Reduce material waste
- Manufacture lightweight, high-strength parts for aerospace and medical use
- Rapidly prototype and test custom designs
2. Applications Across Industries
- Aerospace: Lightweight turbine blades, structural brackets, and engine parts
- Medical: Custom implants and prosthetics tailored to individual patients
- Automotive: High-performance engine components and weight-optimized parts
The use of titanium in additive manufacturing isn’t just a trend—it’s a cornerstone of Industry 4.0, where digital design meets physical production in a seamless, efficient workflow.
CNC Machining and Fabrication of Titanium
Despite its advantages, titanium is notoriously difficult to machine due to its low thermal conductivity and high reactivity at elevated temperatures. However, advanced CNC machining techniques have evolved to overcome these challenges.
1. Specialized Cutting Tools and Strategies
- Coated carbide tools and high-speed steel are optimized for titanium cutting
- Coolant systems help dissipate heat and reduce tool wear
- High feed rates and low cutting speeds are used to prevent tool degradation
2. Hybrid Manufacturing Approaches
Modern manufacturers are combining additive and subtractive methods to:
- 3D print near-net shapes
- Finish them with precision CNC machining This hybrid approach reduces material waste and production time while maintaining tight tolerances and high surface finishes.
Titanium Alloys and Heat Treatment in Advanced Production
Advanced manufacturing isn’t just about shaping titanium—it’s also about engineering the perfect alloy for each application. Titanium’s properties can be enhanced through alloying and heat treatment.
1. Common Titanium Alloys:
- Ti-6Al-4V: The most popular alloy, known for its excellent strength and corrosion resistance
- Ti-6Al-7Nb: Used in medical implants due to its biocompatibility
- Beta titanium alloys: Highly formable and used in sports equipment and advanced prosthetics
2. Heat Treatment for Performance Optimization
- Annealing relieves internal stresses and improves ductility
- Solution treatment and aging (STA) enhances strength and hardness
- Thermomechanical processing refines grain structure for fatigue resistance
These heat treatments allow manufacturers to tailor titanium components for the exact performance requirements of their industries.
Titanium in Tooling and Mold Making
Titanium’s strength and thermal stability also make it a top material in tooling, die casting, and mold making for advanced manufacturing.
Benefits of Titanium in Tooling:
- Longer tool life due to wear resistance
- Stable mold temperature control with minimal distortion
- Compatibility with high-pressure and high-speed injection processes
In industries like aerospace composites and injection molding, titanium tools help achieve greater dimensional accuracy and process efficiency.
Sustainability Through Titanium-Based Manufacturing
Sustainability is now a major focus across all industries, and titanium is playing a pivotal role in reducing environmental impact through advanced manufacturing.
1. Energy Efficiency
Titanium’s lightweight strength leads to fuel and energy savings in transportation and aerospace sectors, especially when used in vehicles or aircraft to reduce mass.
2. Zero-Waste Manufacturing
Additive manufacturing with titanium allows for near-zero waste production, minimizing the use of raw materials and reducing the need for excess energy and resources.
3. Full Recyclability
Titanium is 100% recyclable. Manufacturing processes now incorporate closed-loop recycling systems that reprocess scrap titanium into new parts, supporting circular economy models.
Challenges in Working with Titanium—and How They’re Being Solved
While titanium is a game-changer in advanced manufacturing, it’s not without challenges:
1. High Cost of Raw Material
Titanium is more expensive than many other metals, both in raw form and processing. However, cost-effective extraction techniques such as the FFC Cambridge process and recycling innovations are steadily reducing these barriers.
2. Complex Processing Requirements
Titanium’s sensitivity to oxygen and heat makes it difficult to weld and machine. Modern manufacturing counters this with:
- Controlled atmospheres for welding
- Automated CNC systems
- Laser and electron beam technologies for precise joining and additive layering
3. Equipment Wear and Tear
Due to its hardness and abrasiveness, titanium can wear down tools rapidly. Manufacturers now use advanced coatings, better tool materials, and optimized cutting fluids to extend tool life and lower maintenance costs.
Future Innovations in Titanium Manufacturing
The evolution of titanium in manufacturing is far from over. Researchers and engineers are exploring cutting-edge applications and process improvements:
1. Titanium Matrix Composites (TMCs)
These next-gen materials blend titanium with ceramic reinforcements, offering:
- Even higher temperature resistance
- Enhanced wear properties
- Potential use in hypersonic aircraft and next-gen turbines
2. Nano-Titanium Materials
Nanostructured titanium materials promise unprecedented strength-to-weight ratios, ideal for microfabrication, medical nanodevices, and electronics.
3. AI-Driven Manufacturing
Artificial intelligence is now being integrated with titanium manufacturing to:
- Optimize tool paths and machining parameters
- Predict material behavior
- Reduce production time and increase precision
Conclusion: Titanium at the Heart of Manufacturing Innovation
Titanium’s journey from exotic aerospace material to mainstream manufacturing marvel has been marked by innovation, adaptability, and sustainability. As advanced manufacturing techniques continue to evolve, titanium remains a cornerstone material—supporting everything from 3D printing breakthroughs and precision CNC machining to green manufacturing and future-ready composites.
Its unmatched combination of mechanical performance, corrosion resistance, and adaptability makes it essential for companies seeking to stay ahead in the age of smart manufacturing and sustainable design. Whether you’re building the next generation of medical implants, supersonic jets, or zero-waste factories, titanium isn’t just part of the process—it’s driving the revolution.
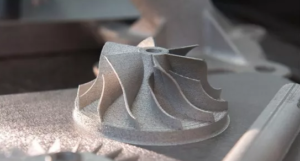
Also Read :