As the aerospace industry enters a new era defined by hypersonic travel, space tourism, and interplanetary exploration, the demand for materials that can withstand extreme conditions while offering optimal performance has never been greater. At the forefront of this technological revolution stands titanium—a material that has become synonymous with high strength, low weight, and exceptional resilience.
From the fuselages of next-generation aircraft to the propulsion systems of deep space missions, titanium continues to shape the future of aerospace engineering. Its unique characteristics have already enabled significant advancements, and as new technologies emerge, titanium is set to play an even greater role in pushing the boundaries of what’s possible in aviation and space travel.
In this article, we explore the evolving role of titanium in aerospace engineering, current innovations, and what lies ahead in this high-stakes, high-altitude industry.
Why Titanium Is Indispensable in Aerospace Engineering
Titanium has long been a staple in aerospace engineering thanks to its exceptional strength-to-weight ratio, corrosion resistance, and heat tolerance. These attributes make it ideal for aircraft and spacecraft components that must perform reliably under extreme stress, high temperatures, and in corrosive environments such as the upper atmosphere or space vacuum.
Core Advantages of Titanium:
- High Strength, Low Weight: Titanium is as strong as steel but 45% lighter—crucial for reducing aircraft weight and improving fuel efficiency.
- Thermal Stability: Maintains structural integrity at temperatures up to 600°C (1,112°F), ideal for jet engines and hypersonic flight.
- Corrosion Resistance: Does not degrade in the presence of moisture, salt, or extreme atmospheric conditions.
- Fatigue and Creep Resistance: Performs well under repeated stress and over long periods—vital for flight-critical components.
These benefits make titanium a top choice for airframes, engine parts, landing gear, fasteners, and shielding systems
Titanium in Modern Aerospace Applications
Titanium is already widely used in both commercial and military aviation, as well as in the development of spacecraft and satellites.
1. Aircraft Structures
Modern aircraft, including the Boeing 787 Dreamliner and Airbus A350, incorporate significant amounts of titanium in:
- Wing structures
- Landing gear components
- Engine pylons
- Hydraulic tubing and fasteners
These titanium components help reduce overall aircraft weight, leading to lower fuel consumption and enhanced flight performance.
2. Jet Engines
Titanium is used in compressor blades, discs, and casings in jet engines due to its ability to withstand:
- High temperatures
- Mechanical stress
- Oxidizing environments
It provides durability without sacrificing efficiency, making it ideal for engines that need to perform under extreme conditions.
3. Spacecraft and Satellites
Titanium is a critical material in space-bound vehicles, where structural components must endure launch stress, radiation, and temperature extremes. Applications include:
- Satellite frames
- Rocket engine parts
- Heat shields
- Fuel tanks
Its low density and resistance to environmental degradation make it invaluable in long-duration missions and planetary exploration.
Additive Manufacturing: Titanium in 3D Printing
One of the most exciting developments in aerospace engineering is the integration of additive manufacturing (AM), or 3D printing, using titanium alloys.
Benefits of 3D-Printed Titanium in Aerospace:
- Lightweight, complex geometries that reduce material usage and increase performance
- On-demand manufacturing for replacement parts or customized components
- Faster prototyping and iteration for innovative designs
- Reduced waste compared to traditional machining methods
Titanium alloys like Ti-6Al-4V are commonly used in powder-bed fusion and direct energy deposition techniques. These methods enable the production of lightweight yet high-strength parts, such as lattice structures, fuel nozzles, and structural supports
Hypersonic Flight and Titanium’s Expanding Role
As aerospace companies and defense agencies develop hypersonic aircraft and missiles that travel at speeds exceeding Mach 5, materials must withstand extreme thermal and mechanical loads.
Titanium in Hypersonic Systems:
- Nose cones and leading edges experience intense aerodynamic heating; titanium’s heat resistance is essential.
- Airframe skins must survive friction-induced temperatures without deforming.
- Internal engine components benefit from titanium’s fatigue resistance under rapid acceleration and deceleration cycles.
Titanium’s durability and stability under such conditions make it one of the few materials suitable for next-gen hypersonic aerospace vehicles.
Space Exploration: Titanium in Interplanetary Missions
With renewed interest in Moon missions, Mars colonization, and deep space travel, titanium is becoming central to the construction of space habitats, propulsion systems, and launch vehicles.
Applications Include:
- Rocket nozzles and casings that endure combustion and vibration
- Structural frameworks for lunar and Martian bases
- Radiation shields and storage containers for scientific instruments and life support systems
Titanium’s resistance to cosmic radiation and ability to perform in extreme cold make it ideal for long-duration missions and extraterrestrial infrastructure.
Emerging Trends and Future Innovations
The future of titanium in aerospace engineering is being shaped by new alloys, processing techniques, and interdisciplinary innovations.
1. Titanium Matrix Composites (TMCs)
Combining titanium with ceramic or carbon fibers produces super-strong composites that offer:
- Even greater strength-to-weight ratios
- Superior heat resistance
- Enhanced performance in critical aerospace systems
TMCs are under development for turbine engines, landing gear, and advanced space vehicles.
2. Sustainable Titanium Production
Efforts are underway to reduce the environmental impact and cost of titanium production. Innovations include:
- FFC Cambridge process for low-energy extraction
- Recycling titanium scrap into high-grade aerospace materials
- Closed-loop additive manufacturing systems that repurpose excess powder
These developments will make titanium more accessible and sustainable for the growing aerospace market.
3. Smart Structures and Sensors
Titanium is being integrated into smart structures with embedded sensors that monitor stress, temperature, and performance in real-time. These systems improve:
- Predictive maintenance
- Operational safety
- Aircraft lifecycle management
Such intelligent components are crucial for autonomous aircraft and spacecraft of the future.
Challenges and Opportunities
Despite its many benefits, titanium’s use in aerospace engineering is not without challenges:
Challenges:
- High material and processing costs
- Machining difficulties due to titanium’s hardness
- Limited availability of large titanium components
Opportunities:
- Expanding use in urban air mobility (UAM) and electric vertical take-off and landing (eVTOL) aircraft
- Integration in space tourism vehicles
- Increasing demand from defense, satellite, and private space sectors
With the development of faster, cheaper production methods and the rise of 3D printing, these challenges are steadily being overcome.
Conclusion: Titanium at the Core of Aerospace’s Bold Future
Titanium has already earned its place as a cornerstone material in aerospace engineering, but its future role is even more promising. As the industry evolves toward faster, lighter, and smarter aircraft and spacecraft, titanium will remain central to innovation.
From enabling hypersonic travel to supporting off-world colonization, titanium is not just a high-performance material—it’s a strategic asset in the quest to redefine what humanity can achieve in the skies and beyond.
As we look toward the next generation of flight and exploration, one thing is clear: titanium will be flying higher, farther, and faster than ever before.
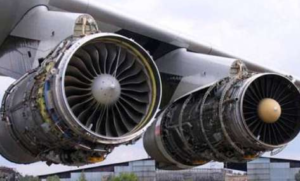
Also Read :