Introduction: Why Titanium is the Backbone of Modern Aerospace
In the world of aerospace engineering, materials matter just as much as mechanics. From soaring commercial jets to stealthy military aircraft and cutting-edge spacecraft, one metal stands out for its unmatched combination of strength, lightness, and resistance to extreme environments—titanium. This extraordinary element has become the material of choice for aerospace manufacturers striving for optimal performance, fuel efficiency, and durability.
Titanium’s impact on aerospace innovation cannot be overstated. Its unique properties continue to redefine the boundaries of what’s possible in flight, space exploration, and defense technologies. This article explores how titanium drives aerospace advancements and why its role is more critical than ever.
The Unique Properties of Titanium
Before diving into titanium’s aerospace applications, it’s essential to understand why this metal is so prized:
- High strength-to-weight ratio: Titanium is as strong as steel but nearly 45% lighter.
- Corrosion resistance: It resists corrosion from air, moisture, and seawater, making it ideal for long-term applications.
- High melting point: Titanium can withstand extreme heat, up to 3,034°F (1,668°C), without compromising structural integrity.
- Biocompatibility: Though more relevant in medical fields, this also supports safer cabin environments.
- Fatigue resistance: Titanium maintains performance under repeated stress, critical for aircraft longevity.
These attributes make titanium a strategic material not only in aerospace but also in defense, automotive, and biomedical sectors.
Titanium’s Rise in Aerospace Applications
A Historical Perspective
Titanium’s aerospace journey began in the 1950s during the Cold War, when the U.S. military sought materials to build faster and higher-flying aircraft. The Lockheed SR-71 Blackbird, for example, famously used titanium for more than 85% of its structure due to its ability to endure the high heat generated at Mach 3 speeds.
Since then, titanium usage has expanded from niche military applications to mainstream aerospace production.
Commercial Aviation: Efficiency and Durability
Modern airliners like the Boeing 787 Dreamliner and the Airbus A350 XWB incorporate large quantities of titanium. It is used extensively in components such as:
- Landing gear
- Engine nacelles
- Fasteners
- Wing structures
- Hydraulic systems
Why titanium? It helps reduce aircraft weight, which translates to improved fuel efficiency and lower emissions—a key concern in the era of sustainable aviation.
Moreover, titanium’s resistance to corrosion minimizes maintenance needs, reducing lifecycle costs for airline operators.
Military Aircraft: Strength Under Pressure
Titanium is heavily utilized in fighter jets, drones, and helicopters where performance under pressure is paramount. For example, the F-22 Raptor and F-35 Lightning II rely on titanium alloys in critical airframe and engine components.
These aircraft must endure high-G maneuvers, supersonic speeds, and hostile environmental conditions—all of which titanium is perfectly suited for.
Spacecraft and Satellites: Defying Gravity and Extreme Conditions
In space exploration, where conditions are harsh, variable, and unforgiving, titanium is a go-to material. NASA and private space companies like SpaceX and Blue Origin incorporate titanium in rockets, spacecraft, and satellite components.
Its light weight reduces launch costs, while its durability and heat resistance ensure mission success in orbit or on interplanetary journeys.
Titanium Alloys: The Secret to Superior Performance
Pure titanium is impressive, but titanium alloys unlock its full potential. These are often blended with elements such as aluminum, vanadium, or molybdenum to enhance specific properties.
The most common aerospace-grade titanium alloy is Ti-6Al-4V, also known as Grade 5 titanium. It offers:
- Superior strength
- Excellent weldability
- High fracture toughness
This alloy is a staple in aircraft engines, landing gear, and structural frames, where performance cannot be compromised.
The Role of Additive Manufacturing (3D Printing)
One of the most exciting trends in aerospace is the rise of additive manufacturing, and titanium plays a central role. Using 3D printing technologies, aerospace firms can now create complex titanium components with minimal waste and enhanced precision.
This method reduces production time, lowers material costs, and opens the door to custom-designed parts that were previously impossible to manufacture using traditional methods.
Titanium and Sustainable Aerospace Development
With the aerospace industry under increasing pressure to decarbonize, titanium’s role is becoming even more crucial. Its lightweight nature contributes directly to:
- Fuel savings
- Reduced carbon emissions
- Improved aerodynamics
Additionally, titanium is highly recyclable, which supports circular economy goals in aviation and space industries. By using recycled titanium in production, manufacturers can cut down on energy-intensive mining and processing operations.
Challenges in Titanium Utilization
Despite its advantages, titanium does come with challenges:
- High cost: Titanium is more expensive to extract and process than aluminum or steel.
- Complex fabrication: Its hardness and reactivity can complicate machining and welding.
- Limited availability: Titanium ores are not rare, but processing capacity can be a bottleneck.
However, ongoing research into advanced smelting techniques and recycling technologies is helping to mitigate these issues.
The Future of Titanium in Aerospace
The future looks bright for titanium in aerospace. Emerging trends and technologies will likely expand its role even further:
- Urban air mobility (UAM): Flying taxis and drones will need lightweight yet robust materials—titanium is an ideal candidate.
- Hypersonic flight: As engineers push for aircraft that travel above Mach 5, titanium’s heat resistance will be invaluable.
- Deep space missions: As humanity ventures further into space, titanium will be instrumental in crafting durable habitats and vehicles.
Moreover, innovations in titanium extraction, alloy development, and manufacturing will continue to unlock new possibilities.
Conclusion: Titanium’s Unmatched Contribution to Aerospace
Titanium isn’t just another metal—it’s a strategic enabler of aerospace innovation. From commercial aviation to defense and space exploration, titanium continues to reshape what’s possible in the skies and beyond. Its blend of strength, resilience, and lightness makes it indispensable for the aerospace industry of today—and even more so for the visionary missions of tomorrow.
As new frontiers emerge, one thing remains certain: titanium will be flying high for decades to come.
If you’d like a version of this article optimized for a specific audience or platform (LinkedIn, blog post, technical white paper), just let me know!
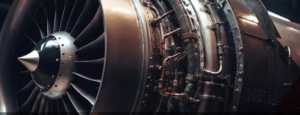
Also Read :