In the realm of advanced materials, titanium has emerged as a game-changer, redefining the boundaries of strength, corrosion resistance, and thermal stability. As one of the most versatile and high-performing metals available, titanium is playing an increasingly vital role in modern metallurgical science, shaping industries from aerospace and defense to biomedical and clean energy technologies.
Titanium’s integration into metallurgy has not only revolutionized traditional manufacturing processes but also inspired the development of new alloys and advanced materials that outperform conventional metals in demanding applications. This article explores the evolving role of titanium in metallurgical science, current research trends, and the innovations that are propelling this exceptional metal to the forefront of the materials world.
Understanding Titanium: A Metallurgical Powerhouse
Titanium is a transition metal known for its unique combination of properties that set it apart from more commonly used metals such as steel, aluminum, and copper:
- High strength-to-weight ratio – ideal for weight-sensitive applications
- Outstanding corrosion resistance – suitable for harsh and reactive environments
- High melting point (~1668°C) – allows use in high-temperature processes
- Biocompatibility – perfect for medical and dental applications
- Low thermal expansion – maintains dimensional stability in extreme conditions
Because of these characteristics, titanium has earned a place as a core material in metallurgical research and industry.
Titanium in Alloy Development
Titanium’s true potential is often unlocked through alloying—the process of combining it with other elements to improve or tailor its properties.
Alpha, Beta, and Alpha-Beta Alloys
Titanium alloys are classified based on their crystal structure:
- Alpha alloys (with elements like aluminum) are stable at high temperatures and offer excellent weldability and creep resistance.
- Beta alloys (with elements like molybdenum or vanadium) are more formable and have higher strength.
- Alpha-beta alloys, such as Ti-6Al-4V, balance strength, ductility, and corrosion resistance and are among the most widely used.
Each class has unique advantages for specific metallurgical applications, from jet engine components to marine structures and biomedical implants.
Applications Across Key Industries
Titanium’s versatility in alloy form has expanded its use across various fields, each demanding specialized metallurgical properties.
1. Aerospace and Defense
In aerospace, weight savings translate directly into fuel efficiency. Titanium’s high strength-to-weight ratio makes it indispensable in:
- Aircraft fuselage and wings
- Jet engine components
- Spacecraft and satellites
- Armor plating for defense vehicles
Titanium alloys used in these applications are engineered for high temperature endurance, impact resistance, and long-term structural integrity.
2. Medical and Dental Metallurgy
Titanium’s biocompatibility allows for safe, long-term use inside the human body. In the medical sector, titanium is used for:
- Surgical implants (e.g., hip, knee, spinal)
- Dental implants and abutments
- Surgical tools and devices
The metallurgical science behind titanium implants focuses on surface engineering to improve osseointegration, reduce wear, and prevent infection.
3. Chemical Processing and Power Generation
Chemical plants and power stations utilize titanium for components that must withstand corrosive environments:
- Heat exchangers and condenser tubes
- Pressure vessels
- Desalination plants
- Geothermal systems
Metallurgists develop titanium alloys to resist corrosion from chlorides, acids, and high salinity, ensuring safe and efficient operations over long service lives.
4. Automotive and Industrial Engineering
In high-performance and electric vehicles, titanium is used to reduce weight and increase component life:
- Exhaust systems
- Suspension springs
- Engine valves
- Structural components
Titanium metallurgy helps meet demands for lightweight strength, reduced emissions, and longer product life cycles.
Advanced Titanium Metallurgy Techniques
Modern metallurgical science continues to push the boundaries of titanium’s capabilities through innovative techniques and processes.
Additive Manufacturing (3D Printing)
Titanium powder is used in metal additive manufacturing to produce complex, lightweight components with minimal waste. Applications include:
- Aerospace brackets
- Customized implants
- Heat exchangers
New research is focused on optimizing powder metallurgy and improving the microstructure of 3D-printed titanium parts for enhanced strength and reliability.
Surface Modification and Coatings
To enhance performance, titanium surfaces are treated or coated using methods such as:
- Anodizing for wear and corrosion resistance
- Plasma nitriding to harden surfaces
- Hydrothermal and sol-gel coatings in biomedical applications
These modifications extend product lifespans and tailor surfaces for specific uses.
Grain Refinement and Nano-Titanium
Nanostructured titanium and ultrafine-grain alloys are being developed to improve:
- Fatigue resistance
- Tensile strength
- Corrosion performance
These advancements in microstructure engineering are creating next-generation materials for extreme environments.
Sustainability and Recycling in Titanium Metallurgy
Despite its many benefits, titanium has historically faced challenges in cost and sustainability due to energy-intensive extraction and processing. However, the industry is rapidly evolving:
Sustainable Titanium Processing
New methods like the FFC Cambridge process allow for lower-energy titanium production from raw ores, reducing environmental impact and production cost.
Titanium Recycling
Scrap titanium, especially from the aerospace sector, is increasingly being recycled into new alloy production. This helps:
- Reduce waste
- Lower costs
- Improve the environmental footprint of titanium metallurgy
These advancements are making titanium a more sustainable option for future metallurgical applications.
Future Outlook: Titanium’s Expanding Role in Metallurgy
With ongoing research and technology development, titanium is expected to play an even greater role in metallurgical science. Areas of expansion include:
- Titanium-aluminide intermetallics for high-performance engine parts
- Titanium foam structures for biomedical scaffolding
- Smart titanium alloys with shape-memory or self-healing capabilities
- Titanium matrix composites for ultra-strong, lightweight components
As industries demand more from their materials—higher performance, lower emissions, longer life cycles—titanium’s adaptability ensures it remains at the core of metallurgical innovation.
Conclusion: A Metal for the Modern Age
Titanium has transformed from a rare and costly material to a mainstay of modern metallurgy, enabling advanced engineering and scientific breakthroughs. Its role continues to grow, driven by its unique properties and the expanding capabilities of metallurgical science.
Whether in space, inside the human body, or deep in the ocean, titanium is forging a new era of high-performance materials that align with the demands of our modern world—stronger, lighter, safer, and more sustainable.
SEO Keywords: titanium metallurgy, titanium alloys, advanced titanium materials, titanium in aerospace, titanium medical applications, titanium alloy properties, sustainable titanium production, titanium recycling, titanium 3D printing, titanium in chemical engineering
Let me know if you’d like to tailor this article for a specific industry like biomedical, aerospace, or energy metallurgy!
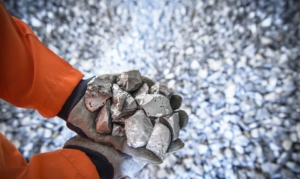
Also Read :