Titanium alloys are pivotal in high-performance engineering and scientific applications due to their unique combination of strength, light weight, and exceptional resistance to extreme environments. As industries continue to demand materials that can endure the harshest conditions while maintaining peak performance, titanium alloys have risen to the challenge. These alloys, which are created by combining titanium with other elements like aluminum, vanadium, and molybdenum, are critical in advancing a wide range of fields including aerospace, automotive, biomedical, and energy sectors.
This article explores the role of titanium alloys in high-performance engineering and science, emphasizing their versatility, unique properties, and growing importance in modern technological innovations.
Why Titanium Alloys Are Ideal for High-Performance Engineering
Titanium alloys are renowned for their high strength-to-weight ratio, which is particularly valuable in applications where both strength and weight are critical factors. These alloys are lightweight yet incredibly strong, which makes them perfect for applications in industries where every ounce of weight matters—such as in aerospace and automotive engineering.
Key Properties of Titanium Alloys:
- High Strength-to-Weight Ratio: Titanium alloys are incredibly strong yet much lighter than many other metals like steel or aluminum.
- Corrosion Resistance: Titanium naturally forms a protective oxide layer that shields it from corrosion, even in harsh environments like seawater, acid, and high-temperature conditions.
- Heat Resistance: Many titanium alloys retain their strength at high temperatures, which makes them ideal for high-performance engines and components exposed to extreme heat.
- Biocompatibility: Titanium alloys, especially in the biomedical field, are well-suited for medical implants due to their compatibility with human tissue.
These properties make titanium alloys indispensable in the creation of high-performance components that can withstand extreme conditions while maintaining efficiency and reliability.
Applications of Titanium Alloys in Aerospace Engineering
The aerospace industry has long been one of the most significant consumers of titanium alloys, particularly in the manufacture of aircraft, spacecraft, and related components. The need for materials that can withstand the extreme conditions of high-altitude flight and space travel while maintaining strength and lightweight properties has driven the demand for titanium alloys in this sector.
1. Aircraft Components
Titanium alloys are widely used in aircraft structures such as landing gears, wings, and fuselage components due to their strength, fatigue resistance, and low weight. Some of the most commonly used alloys in the aerospace industry are:
- Ti-6Al-4V: A titanium alloy with a mixture of aluminum and vanadium, known for its strength, lightness, and corrosion resistance. It is used in engine components, airframes, and fasteners.
- Ti-3Al-8V-6Cr-4Zr-4Mo: Often used in high-performance turbine engines for its high strength at elevated temperatures.
2. Spacecraft Applications
Titanium alloys are also essential in spacecraft design, where materials must not only handle high temperatures but also be resistant to the vacuum and radiation of space. Titanium aluminide is one alloy that is used in the high-temperature sections of rocket engines due to its ability to maintain structural integrity under extreme heat conditions.
3. Propulsion Systems
Titanium’s high heat resistance makes it ideal for turbine blades, compressors, and other components exposed to extreme temperatures and pressures in both aircraft and rocket engines. The use of titanium allows engineers to design lighter, more fuel-efficient engines, which ultimately leads to cost savings and improved performance.
Titanium Alloys in Automotive Engineering
In the automotive sector, titanium alloys are increasingly being used to improve vehicle performance by reducing weight and enhancing strength, durability, and resistance to heat and corrosion.
1. High-Performance Engine Components
Titanium alloys are used in engine parts such as valves, connecting rods, and pistons, where high strength and low weight are essential for enhancing performance. The use of titanium in these components leads to higher engine speeds, greater fuel efficiency, and better overall power-to-weight ratios. Ti-6Al-4V is commonly used in high-performance engines for sports cars and racing vehicles.
2. Lightweight Structural Components
Titanium is also utilized in the construction of chassis components, suspension systems, and exhaust systems. Reducing the weight of these parts is crucial for improving vehicle handling and fuel efficiency without sacrificing strength or durability. Components such as springs, brake calipers, and frames benefit from titanium’s unique properties.
3. Advanced Performance in Electric Vehicles (EVs)
As electric vehicles grow in popularity, titanium alloys are becoming more integral to reducing the overall weight of EVs. By incorporating titanium in battery housings, heat exchangers, and motors, manufacturers can produce lighter, more efficient electric cars with improved range and energy performance.
Titanium Alloys in Biomedical Applications
One of the most remarkable aspects of titanium alloys is their biocompatibility, making them ideal for use in biomedical devices and implants. Their resistance to corrosion and ability to integrate well with human tissue has made them the material of choice for many medical applications.
1. Orthopedic Implants
Titanium alloys are widely used in hip, knee, and dental implants due to their high strength, lightweight nature, and resistance to corrosion. Ti-6Al-4V, in particular, is commonly used for bone plates, screws, and prosthetics because of its proven reliability in load-bearing applications.
2. Cardiovascular Devices
Titanium alloys are used in pacemakers, stents, and heart valve prostheses. Their corrosion resistance is particularly valuable in medical devices that must remain inside the body for extended periods. Additionally, titanium alloys are often used in vascular grafts, ensuring that the material won’t degrade in body fluids over time.
3. Custom Implants and Prosthetics
With the advancement of 3D printing technologies, titanium alloys are being used to create customized implants and prosthetics tailored to the needs of individual patients. This approach allows for faster recovery times and improved functionality.
Titanium Alloys in Energy Production and Petrochemicals
Titanium alloys also play a vital role in energy production, particularly in the oil and gas industry and nuclear energy production. The materials’ ability to withstand extreme temperatures, high pressures, and corrosive environments makes them essential in these high-risk industries.
1. Offshore Oil and Gas
Titanium alloys are used in offshore drilling rigs, subsea equipment, and piping systems where corrosion from seawater and pressure from deep-sea environments are significant concerns. Ti-6Al-4V and beta titanium alloys are often employed in valves, heat exchangers, and pump components.
2. Nuclear Power Plants
In the nuclear industry, titanium alloys are used in reactor cores, heat exchangers, and cooling systems because they are resistant to corrosion from radioactive materials and high-temperature environments. Their ability to endure harsh conditions while maintaining integrity is crucial for the safety and efficiency of nuclear energy production.
3. Chemical Processing and Desalination
Titanium alloys are used in chemical reactors, distillation columns, and desalination plants due to their resistance to corrosive chemicals and high-temperature environments. They help to ensure that chemical processes can be carried out efficiently and without the risk of material degradation.
Conclusion: The Unmatched Versatility of Titanium Alloys
Titanium alloys have earned their reputation as materials that can meet the most demanding performance standards in engineering, science, and technology. From aerospace and automotive to biomedical implants and energy production, titanium alloys offer an unparalleled combination of strength, durability, and resistance to extreme environments.
As industries continue to evolve and demand materials that can withstand increasingly complex and extreme conditions, the role of titanium alloys in high-performance engineering will only grow more critical. With their continued use in next-generation applications, titanium alloys are poised to remain at the forefront of scientific and technological advancements for years to come.
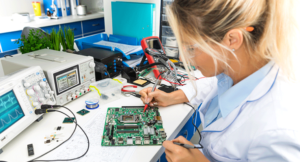
Also Read :